Is A Tube Person Necessary to Protect Pharmacy Ops?
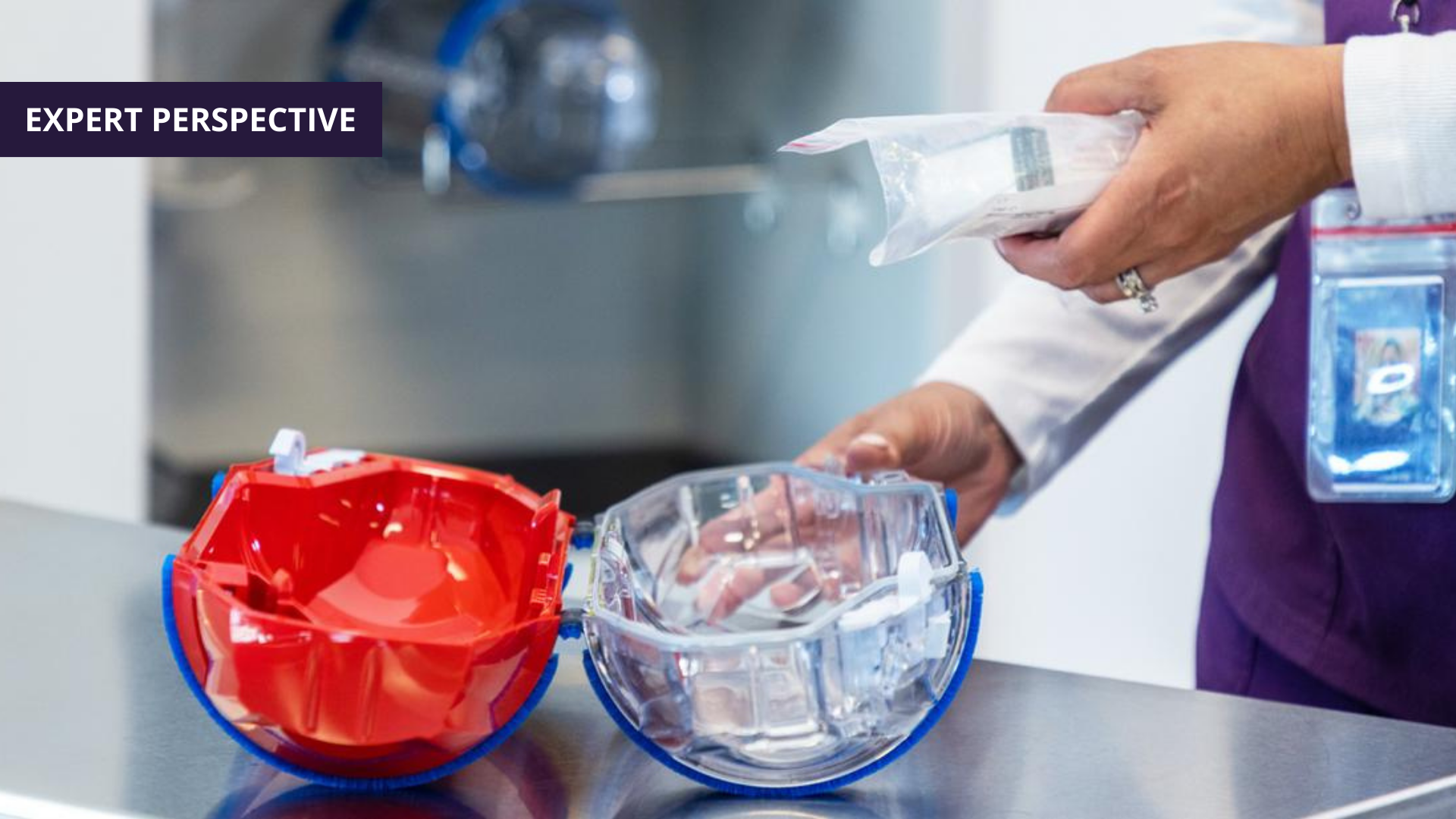
Tube System Failure Can Interrupt Workflow
Over the last few decades thousands of new hospital technologies have come on the market – including operational technology like pharmacy automation. As expected, the more exciting ones have garnered the most attention. Those that have consistently proven their value, however, are the ones most relied upon by hospital IT and facilities managers.
One critical piece of technology that gets less attention but has become a staple in most hospitals is the pneumatic tube system. These are the systems hospitals depend on to connect all wards, surgical rooms and departments with the hospital’s laboratory and central pharmacy. Pneumatic tube systems significantly shorten the delivery times of sensitive materials and medications throughout the hospital. Without them, operations can slow dramatically – especially in the case of the pharmacy.
How well are you maintaining your hospital’s pneumatic tube system?
Because pneumatic tube systems have proven their reliability as workhorses, hospital facilities managers and IT professionals often neglect to put sufficient attention on maintaining them. It is understandable given the workloads these professionals sustain on a day-to-day basis. However, maintenance of these systems is key to helping avoid serious medication transport issues.
Maintenance typically involves several areas. Keeping the software up to date is essential as well as taking advantage of updates and upgrades to ensure that the switches, stations, and crossings meet the latest technological standards. Any issues must be resolved quickly to keep the pneumatic tube systems working and materials moving.
Proper maintenance and support of these systems is critical because any issue at any point in the tube network can quickly immobilize the entire system. When this occurs, automated, secure movement of sensitive materials and medications comes to a standstill. As a result, hospitals must rely on manual transport which is less accurate and secure than using the tube system.
What happens after a tube system failure can quickly become costly to the hospital management who must do one of the following:
- Schedule an expert in pneumatic tube systems to come onsite to fix the issue. This will be less costly if the hospital is equipped to accept remote access.
- Reassign highly compensated medical staff to walk materials and medications back and forth across a busy hospital campus.
- Pay an agency to provide couriers to transport the materials.
- Work to mitigate the negative impact on patients of delayed medications, diagnoses, and treatment.
Who is in charge of keeping your pneumatic tube system working efficiently?
Many hospitals rely upon their IT or facilities management people to maintain their pneumatic tube systems and step in and fix a malfunction. However, this may present its own set of issues including:
- Availability. Are they on/off shift, on leave, or working to solve another critical issue?
- Knowledge. How up to date are they with the intricacies of your tube system? Are they trained to conduct regular system checks to keep the tube system operating effectively?
- Time loss. How much time are they spending attempting to locate where the failure occurred and figuring out how to fix it?
- Resources. Who will they contact for more information and what is their availability?
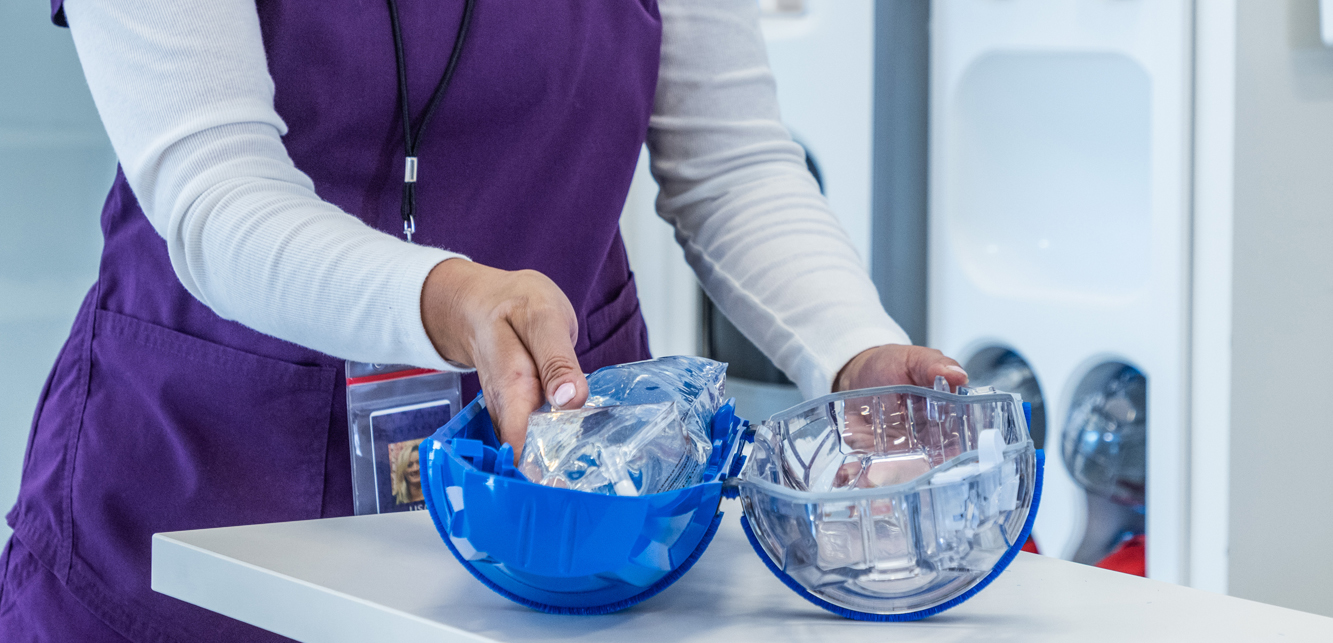
What is your plan?
To minimize downtime hospitals need fast access to experienced pneumatic tube system technicians. Here are some of the options available:
- Dedicated on-site pneumatic tube technician. Having a “tube guy” on site, while more costly, will ensure that your pneumatic tube system is well maintained and that possible issues are resolved well ahead of causing any system failures.
- Local field service engineer relationship. Less costly than a dedicated FTE, but subject to the availability of experienced technicians. Look for a supplier who provides regular training and utilizes new technologies, such as AI to diagnose and resolve issues more efficiently.
- Trained staff onsite. This involves training existing hospital IT or facilities managers on the pneumatic tube system, adding its maintenance to their existing responsibilities. How effective this is will depend on their existing workloads and the frequency of staff turnover.
Don’t neglect the importance of preventative maintenance.
One of the best ways to avoid issues with your pneumatic tube system is to obtain a preventative maintenance agreement from your supplier. That agreement should provide the following:
- A certified technician employed and trained by the manufacturer of your system.
- Opportunities for parts discounts
- Regular software updates to address security risks as well as provide new features and releases.
What is the best fit for your hospital?
Under consideration should be the size of your hospital, the complexity of your services and patient needs, and how reliant you are on your pneumatic tube system. For instance, do you operate from a centralized pharmacy? Do you deal with radiopharmaceuticals that have strict handling and timing constraints? Do you have the staff to manage inefficiencies caused by the rippling effect of tube system malfunction? Collaboration between hospital IT leadership, hospital facilities managers and other key stakeholders can help determine this.
Running scenarios and analyzing their impact on hospital operations can help put the right plan together for your hospital. Your management team can work together to assess a variety of possible backup plans, and what each involves from an operational and expense standpoint. Most importantly, the impact of a failure on medical staff and other employees should be considered.
Don’t wait for a tube system failure to act.
Now is the time to put a plan together that provides immediate access to the level of expertise needed to ensure that your pneumatic tube system is well maintained, and issues quickly resolved.
Don’t wait for a failure to occur. A system failure means instant downtime which impacts everyone in the hospital at all levels, including patients. It can quickly become time consuming and expensive to identify and fix the issue, as well as resorting to alternative means of materials transport.
Pneumatic tube systems will continue to play a critical role in a hospital – especially in the pharmacy. Make sure you are taking maintenance of these critical systems seriously and planning accordingly. You’ll be glad you did.