Correct Consumables: Why They Matter
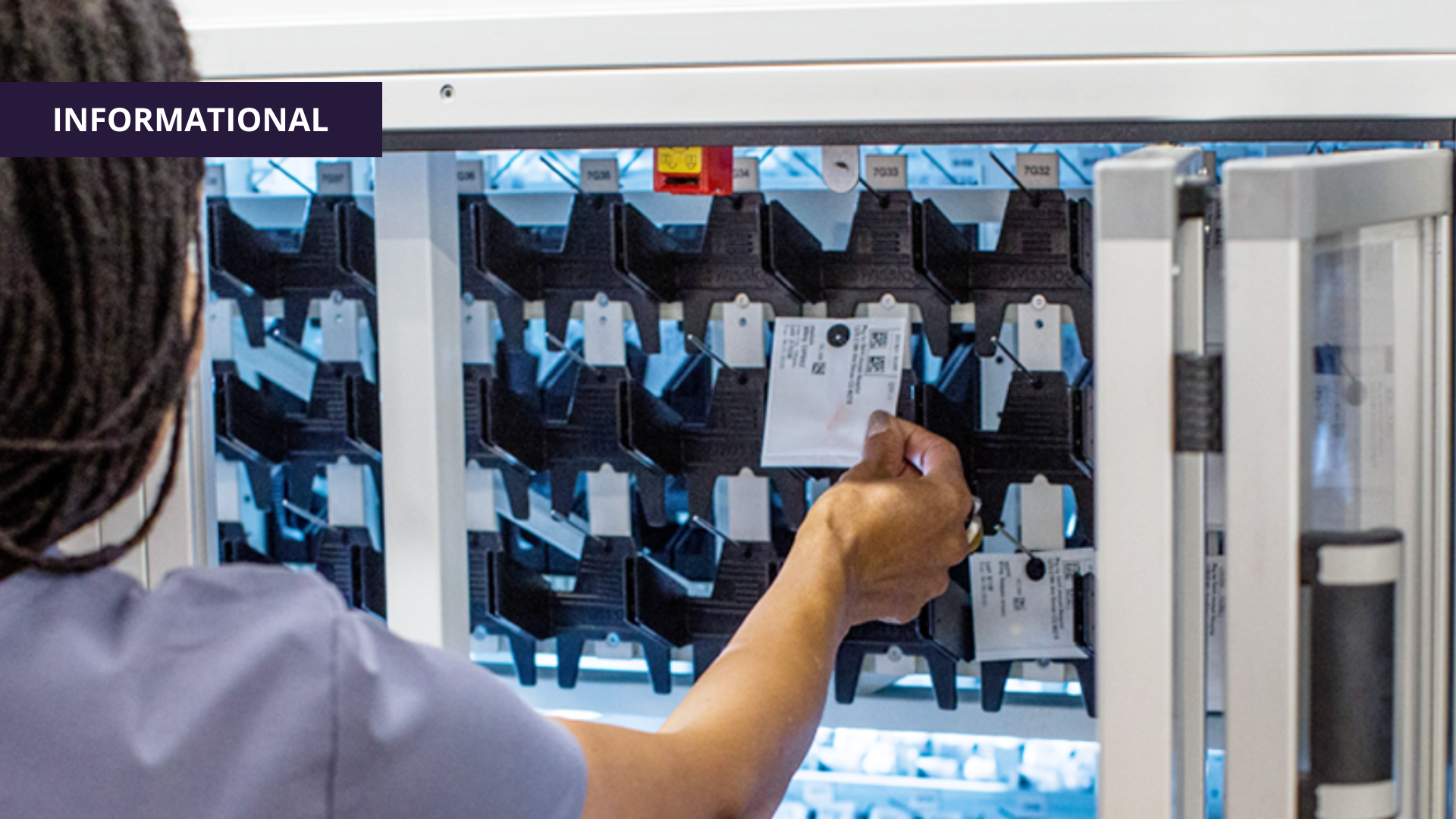
Pharmacy Automation Solutions Need Proper Care
Innovative technologies have found their way into an increasing number of hospital pharmacies throughout the world. Procedures that used to be time-consuming and prone to human error are now being automated using new technologies that improve the accuracy and security of medications procurement, management, and dispensation.
Many of today’s pharmacy automation platforms have implemented the use of robotics to handle medications management quickly and efficiently. Each unit dose of medication is packaged, labeled, and ready for administration by authorized personnel.
Hospital Pharmacies Rely Upon Consumables For Unit Dose Packaging
The robotic automated process of preparing medication for use and packaging medications has many moving parts. The systems must be stocked with an array of consumables which may include the following:
- Mechanical components including straws and suckers.
- Packaging materials including paper, printer ribbon, and labels.
These consumables are critical to ensuring that the correct medication in the correct amount is dispensed to the right patient at the right time. Any variation that occurs can disrupt the process and impact the health of the patient.
How Can Consumables Disrupt An Automated Hospital Pharmacy?
Most of the time, operational issues arising in a pharmacy using automation are due to compatibility issues arising from supplies purchased from a discounted source or getting a “deal” from an off-brand provider. Here are some of the issues that can arise:
- Smudged printing on labels: This can occur when an incorrect ribbon is being used which is not compatible with the pharmacy printer. These labels can potentially be misread which can result in serious errors in medications dispensation.
- Printer jams: Using labels that are not compatible with the printer can cause jams which in turn require a support technician to shut down the system and track down where the jam occurred.
- System shutdown: When consumables are not properly calibrated to the system a complete shutdown may occur to avoid system damage. When this happens a maintenance call is needed. The system could potentially be down for hours or even days.
- Void a service contract: Many vendors will no longer honor a service contract if the customer turns to other manufacturers for their consumables. There are too many potential issues that can arise, which could compromise their service.
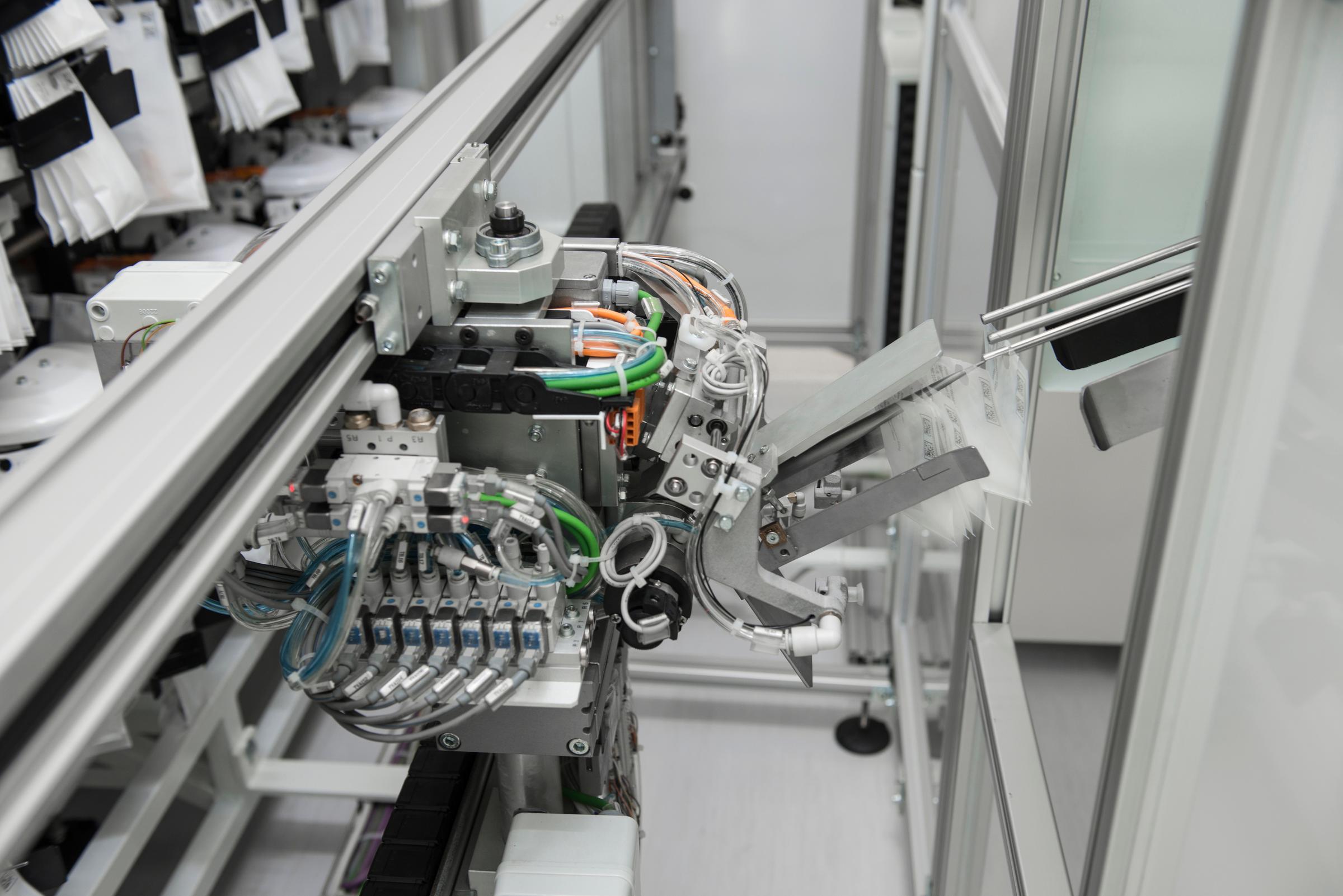
Depleted Consumables Can Also Create Issues In Pharmacy Operations
It is important for hospital pharmacies to keep their supply inventory up to date. Not doing so can quickly bring systems to a standstill. When a pharmacy runs out of straws, as an example, a pharmacy employee must find ways to secure additional supplies either from other areas of the hospital or emergency supplies from the provider. This takes time and can instantly impact performance and service to patients. Rush orders can be costly as well.
Using The Correct Consumables Makes A Big Difference In Pharmacy Efficiency
The good news is that proper planning and working with your original supplier can make a big difference in the working order of your hospital pharmacy. Most issues can be avoided by doing the following:
- Ensure that all consumables are purchased from the original supplier. That will ensure compatibility and optimize the working order of all components.
- Ensure that all consumables are replenished regularly. This involves not only understanding your average usage, but always having extra supplies on hand to deal with special circumstances such as long weekends or a disruption in your supply chain.
- Ensure that a support agreement is in place which includes regular system maintenance as well as troubleshooting any issues.
Hospitals Will Always Seek Areas To Cut Costs And Save Time
It is important for pharmacy personnel to understand that the components of your hospital pharmacy are calibrated to use specific styles and types of consumables. The slightest change in paper, ribbons, labels, and mechanical components can result in a disruption that can have a major impact on quality of care provided to patients. It may also require your pharmacy personnel to revert to manual processes that will create added delays.
Hospitals continue to be under enormous pressure to provide quality care while remaining within tight budgets. It is understandable that management looks for ways to save money on supplies. Doing so with pharmacy automation tools and consumables can lead to serious disruption that can take days and weeks to recover from.
Make sure that your consumables are calibrated to perfectly fit your pharmacy platform. You will be rewarded with a system that runs smoothly and efficiently, saving time for your employees and delivering correct and timely medications to your patients.